Instructions for the operation of double-sided grinder
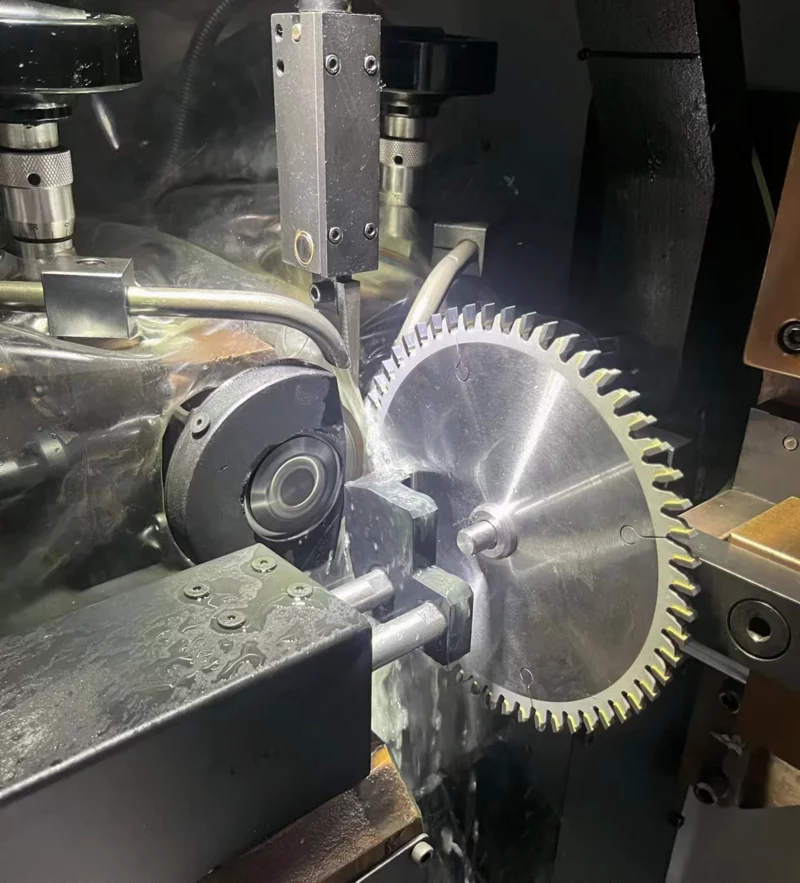
I. Operation procedure
1. Turn on the power switch.
2. Turn on the hydraulic switch, press the stop button to reset the machine's grinding head.
3. Start the machine and let it idle for two minutes to check if everything is normal.
4. Measure the thickness of the saw blade and adjust the center position (the alignment of the center line of the saw blade with the center of the grinding wheel). Before starting each shift, the machine must be aligned.
5. Choose the appropriate core sleeve according to the inner hole of the saw blade (the gap between the inner hole and the core sleeve meets the tolerance requirements).
6. Mount the saw blade onto the push rod, adjust the distance between the saw blade and the chip breaker, and check if the chip breaker is normal.
7. Adjust the stroke of the grinding wheel to the alloy of the saw blade, and check if the grinding wheel finishes the alloy and retreats just enough of the alloy's top. Lock the stroke once the required stroke is achieved.
8. Adjust the angle of the saw blade according to the requirements of the processing sheet (back rake angle, side rake angle).
Back rake angle: Turn clockwise from zero to the zero position.
Side rake angle (left): Turn clockwise from zero to the zero position.
Side rake angle (right): Turn counterclockwise from zero to the zero position.
9. Start automatic trial grinding on a few teeth, check if the angle matches the drawing. If it does, proceed with normal processing.
10. Increase the amount of grinding fluid to jet onto the contact surface between the grinding wheel and the alloy to prevent damage to the grinding wheel and alloy.
II. Process requirements, quality control requirements
1. The protrusion tolerance: -0.02~0.04mm.
2. The protrusion tolerance fluctuation: 0.02mm.
3. Tolerance of side rake angle and back rake angle: ±0.01°.
4. Tolerance for reducing the side flatness: ±0.03mm.
5. Strictly control the amount of grinding each time, less than 0.02mm.
6. Select the appropriate feed rate according to the grit size of the grinding wheel.
7. When the clamp scratches the saw blade, repair or replace it in a timely manner.
III. Maintenance precautions
1. Clean the equipment before and after work.
2. When starting the machine, drain the water from the air trio, check if the oil in the trio is near the minimum oil level line, and replenish pneumatic oil when it reaches the minimum oil level line.
3. Check if there is enough grease in the automatic oiling system, replenish ESSOS420 grease or a similar specification and model of another brand if insufficient.
4. Coat the rust-proof oil on the saw blade core sleeve that is not in use for the time being.
5. Clean the dirt in the water tank and clean the filter and water pump every time the grinding fluid is replaced.
6. Check if the hydraulic pressure is between 30~40Kg, the air pressure is between 4~6bar, and check for any water, air, or oil leakage. Also check if the hydraulic oil level is lower than the minimum oil level line, and replenish the hydraulic oil immediately if it is insufficient.
7. The equipment accuracy should be checked at least once a week to meet the requirements.
With years of hands-on experience, I have honed my skills in navigating the complexities of global commerce, offering invaluable insights and solutions to address customer needs. My commitment to excellence and dedication to customer satisfaction ensure that I deliver exceptional service, guiding clients through every step of the trading process with confidence and proficiency.