JS350 Double side grinding machine(Robotic arm)
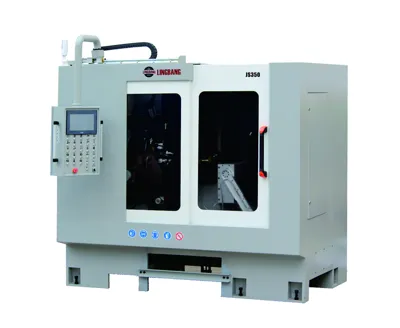
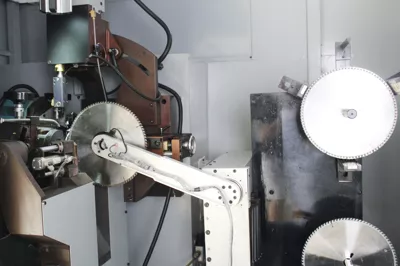
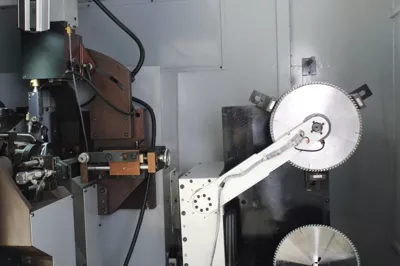
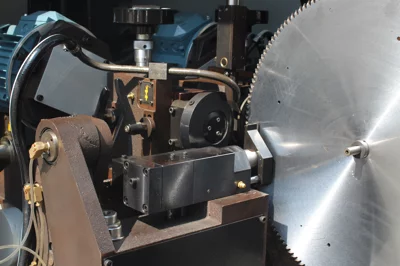
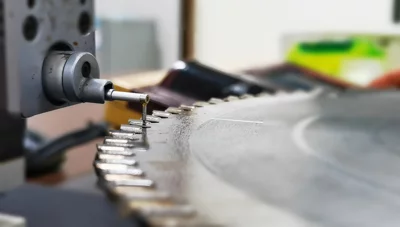
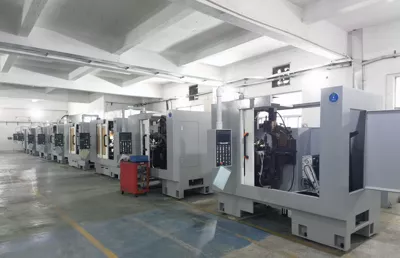
Basic Attributes
- Blade Outside diameter 120-360 mm
- Bore hole diameter 20-60 mm
- Max blade thickness 8 mm
- Tooth Pitch 7-60 mm
- hook angle -15°~+30° °
- radial angle -4°~6° °
- tangential angle from 0 0 0 to +6 +5 +4 °
- Max Grinding Stroke 15
- Grinding speed 0.5~6 mm/s
- Grinding wheel outside dia. 80/100/125 mm
- Grinding wheel linear speed 23/28/35 mm
- Coolant tank capacity 200 L
- Total power 5.5 kW
- Machine Size 2150*1780*2100 mm
- Package size 2280*1930*2260 mm
- Machine Weight 2,100 kg
A wide range of applications,including iron dry cutting saw blades, aluminum alloy saw blades, woodworking saw blades and plastic PVC industrial features.
Machine structure and moving parts of high strength QT500 ductile iron materials.
The spindle is imported products, with high precision, high strength, high rigidity and high speed (2-year warranty).
Equipped with CNC automation control system and servo tool and feed system.
Open program design, can meet various needs, and provides multiple sets of reciprocating grinding program.
The manipulator adopts full servo screw drive mode, with higher accuracy, stability and rigidity.
Overall protective shell, beautiful and environmentally friendly.
Full servo tool setting, feed system, and machine adjustment tool setting are simple, convenient, easy to learn, and easy to masterFull servo manipulator (more stable without pneumatic), ensuring higher stability and accuracyGrinding accuracy thickness tolerance ≤0.01mmOne-year warranty for the whole machine
The high-precision servo mechanical hand is composed of the X axis, Y axis, and servo planetary motor.
The high-precision servo mechanical hand has four working positions: grinding position (position where the saw blade is being ground), finished product position (position where the saw blade is placed after grinding), waiting position (position where the mechanical arm is waiting while the main machine is operating).
Mechanical hand adjustment operation process:
1. Use the high-precision servo to rotate the mechanical arm and align it with the center hole of the material taking position. Then, the Z-axis of the mechanical hand moves back and forth (controlled by a stepper motor) to the saw blade position. The touch screen is used to activate the electromagnet, causing the saw blade to be adsorbed onto the electromagnet of the mechanical arm. Save each coordinate.
2. Adjust the Z-axis to move the saw blade away to the zero position of the Z-axis.
3. Rotate the mechanical arm to move the mechanical part to the grinding position, and then adjust the X-axis of the mechanical hand (moving left and right) to align the center hole of the saw blade with the core sleeve. Save each coordinate.
4. Adjust the Z-axis of the mechanical hand to bring the saw blade close to the position of clamping the carbide sheet. Save each coordinate.
5. The mechanical arm adsorbs the saw blade and moves out of the grinding position, then rotates the swing arm to the feeding position. Align the center hole of the saw blade and the feeding rod to be concentric. Adjust the Z-axis stroke. Save each coordinate.
For more information about alloy circular saw blade manufacturing equipment, please click