Operation Procedures for Double-Sided Grinding Machine
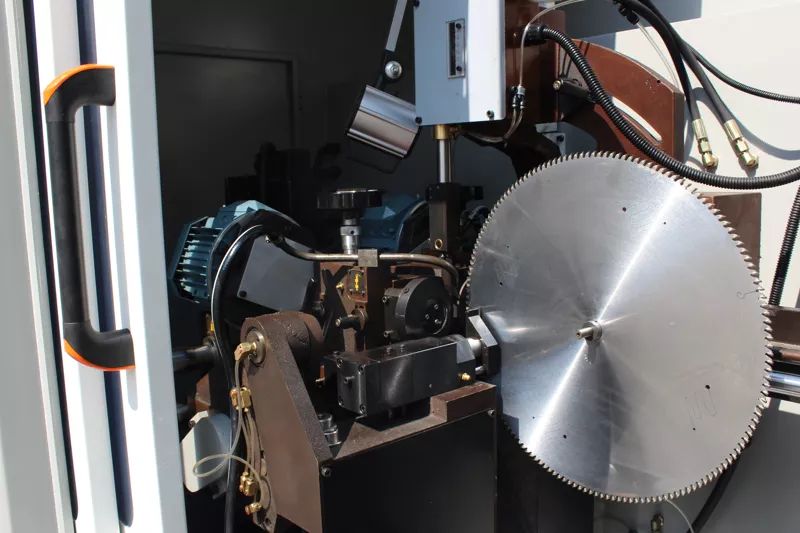
1. Turn on the power switch.
2. Turn on the hydraulic switch, press the stop button to reset the machine head.
3. Start the machine and let it idle for two minutes to check if everything is normal.
4. Measure the thickness of the saw blade and adjust the center position (align the center line of the saw blade with the center of the grinding wheel), align it before each test grinding in the shift.
5. Choose the appropriate bushing based on the inner hole of the saw blade (the gap between the inner hole and the bushing meets the tolerance requirements).
6. Install the saw blade on the push rod, adjust the distance between the saw blade and the tooth head, and check if the tooth head is normal.
7. Adjust the travel of the grinding wheel to the alloy of the saw blade, making sure the grinding wheel passes the alloy and retreats just to the top of the alloy. Once the required travel is reached, lock the travel.
8. Adjust the angle of the saw blade according to the requirements of the processing order (back angle, side angle).
Back angle: Turn clockwise from zero to zero position.
Side angle (left): Turn clockwise from zero to zero position.
Side angle (right): Turn counterclockwise from zero to zero position.
9. Turn on the automatic test grinding for a few teeth, measure whether the angle matches the drawing, and proceed with normal processing if it matches.
10. Spray a larger amount of grinding fluid to the contact surface of the grinding wheel and alloy to prevent damage to the grinding wheel and alloy.
Process requirements, quality control requirements
1. Extrusion tolerance: -0.02 to 0.04mm.
2. Extrusion jump tolerance: 0.02mm.
3. Tolerance of back angle and side angle: ±0.01°.
4. Side flatness reducing tolerance: ±0.03mm.
5. Strictly control the single grinding amount, each time less than 0.02mm.
6. According to the granularity of the grinding wheel, choose the appropriate feed speed.
7. When the clamp scratches the saw blade, it should be repaired or replaced in time.
Maintenance precautions
1. Clean the equipment before and after work.
2. Every time the machine is turned on, drain the water from the air triplex and check if the oil in the triplex is near the minimum oil level line. If it is at the minimum oil level line, top up with pneumatic oil.
3. Check if the grease in the automatic lubrication system is sufficient. If not, refill with ESSOS420 grease or similar specification grease from other brands.
4. Saw blade bushings not in use should be sprayed with rust preventive oil for storage.
5. When replacing the grinding fluid, clean the dirt in the water tank and clean the filter and water pump.
6. Check if the hydraulic pressure is between 30-40Kg, the air pressure is between 4-6bar, inspect for any leaks of water, air, or oil, and check if the hydraulic oil level is below the minimum oil level line. If below, immediately refill with hydraulic oil.
7. The equipment accuracy should be checked at least once a week to meet the requirements.
With years of hands-on experience, I have honed my skills in navigating the complexities of global commerce, offering invaluable insights and solutions to address customer needs. My commitment to excellence and dedication to customer satisfaction ensure that I deliver exceptional service, guiding clients through every step of the trading process with confidence and proficiency.